Updated energy code has been adopted- goes into effect April 27th 2025.
State electric ready code has been adopted too.
Link to 4-27-2025 adoption text
New construction:
The prescriptive 2021 IECC table has been modified. Most notably .27 U-factor windows mandatory.
New Performance path/ERI/HERS goals: 2021 HERS-PV / HERS+PV
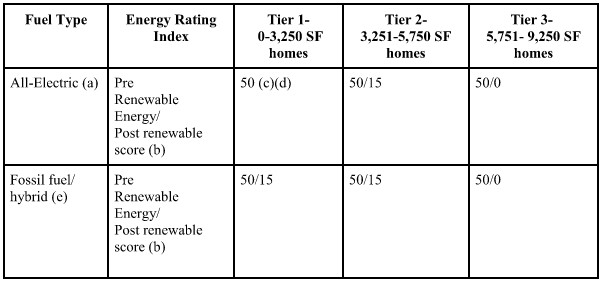
Note that off-site solar is allowed in some circumstances.
All PV requires an energy storage system of 5 kWh or 25% of annual production, whichever is greater.
All projects are requested to provide a release of utilities provider information so usage can be tracked.
Additions:
New building envelope assemblies that are part of the addition shall comply with Section R402. (projects can still use UA trade-off)
Additions of 500 square feet or more of floor area shall be divided into two categories and include
the following additional requirements:
Tier 1 dwellings (0-3,250 sf, existing + new): shall be required to conduct a pre-construction
Home Energy Assessment by a certified third party on the existing building. A comprehensive
report of the assessment shall be submitted with the building permit application and include the
following criteria:
1. Annual Energy Consumption
2. Existing Building Envelope Air Leakage Test
3. Recommended Building Envelope Upgrades
4. Recommended HVAC Upgrades
5. Recommended Water Heating Upgrades
6. Recommended Health and Safety Upgrades
7. Recommended Lighting and Appliance Upgrades
A post-construction Air Leakage Test shall be performed on the existing building and addition prior
to Final Building Inspection demonstrating a 15% reduction in air leakage.
Tier 2 dwellings (3,251 sf and above, existing + new): shall be required to conduct a pre-construction
Energy Rating Index Assessment performed in accordance with ANSI/RESNET/ICC
301, on the existing dwelling, as well as a projected rating including the addition to document any
level of improvements made and to ensure that the home does not perform worse than it did prior to
the addition in accordance with Section R502.1. In addition to the Energy Rating Index, a
comprehensive report of the assessment shall be submitted with the building permit application and
include the same criteria as in Tier 1. A post construction assessment shall be submitted prior to
Final Building Inspection to demonstrate compliance. A post-construction Air Leakage Test shall
be performed on the existing building and addition prior to Final Building Inspection demonstrating
a 15% reduction in air leakage.
Exception: New envelope assemblies in additions less than 500 square feet in area are exempt from
the requirements of Section R402.4.1.2, R402.4.1.3.
Alterations:
Building envelope assemblies that are part of the alteration shall comply with Section R402. (projects can still use UA trade-off)
Alterations of 500 square feet or more of floor area shall be divided into two categories and include
the following additional requirements:
Tier 1 dwellings (0-3,250 sf): shall be required to conduct a pre-construction Home Energy
Assessment by a certified third party on the existing building. A comprehensive report of the
assessment shall be submitted with the building permit application and include the following
criteria:
1. Annual Energy Consumption
2. Existing Building Envelope Air Leakage Test
3. Recommended Building Envelope Upgrades
4. Recommended HVAC Upgrades
5. Recommended Water Heating Upgrades
6. Recommended Health and Safety Upgrades
7. Recommended Lighting and Appliance Upgrades
A post-construction Air Leakage Test shall be performed on the existing building and alteration
prior to Final Building Inspection demonstrating a 15% reduction in air leakage.
Tier 2 dwellings (3,251 sf and above): shall be required to conduct a pre-construction Energy
Rating Index Assessment performed in accordance with ANSI/RESNET/ICC 301, on the existing
dwelling, as well as a projected rating including the alteration to document any level of
improvements made and to ensure that the home does not perform worse than it did prior to the
proposed alteration in accordance with Section R503.1. In addition to the Energy Rating Index, a
comprehensive report of the assessment shall be submitted with the building permit application and
include the same criteria as in Tier 1. A post construction assessment shall be submitted prior to
Final Building Inspection to demonstrate compliance. A post-construction Air Leakage Test shall
be performed on the existing building and addition prior to Final Building Inspection demonstrating
a 15% reduction in air leakage.
Exception: Alterations defined below shall not be required to comply with the required assessments
of this section provided that the energy use of the building is not increased.
1. The removal and replacement or the covering of existing materials, elements, equipment or
fixtures using new materials, elements, equipment or fixtures that serve the same purpose.
2. The addition or elimination of any door or window, the reconfiguration or extension of any
system, or the installation of any additional equipment, and shall apply where the work area
is less than 500 sf floor area.
3. Alterations exposing or demolishing more than 75% of the building’s thermal envelope area
shall comply with the energy requirements of Section R407
Renewable Energy Mitigation Program (REMP) Calculators:
REMP (XLS)- Version 2025- Coming April 2025 https://pitkincounty.com/192/Building
Effective 12-15-2023
- County-wide cap on home size; 9250 square feet.
- Some special areas have a smaller cap at 8250 or 5750 sf.
https://pitkincounty.com/1566/Pitkin-County-Code-Updates
Effective 3-13-2024
- 2021 IECC
- Title 11.32 adopts an exterior energy budget of 200 Million Btu’s, 6000 sf snowmelt cap
- Title 11.34 adopts electric ready provisions; homes must be EV ready and must use electric for heating, cooling and water heating, or provide the electrical infrastructure to convert to electric in the future.
https://pitkincounty.com/DocumentCenter/View/32664/2024-Energy-Code
Confluence Architecture & Sustainability can help with REMP calculations and provide all the documentation, modeling, testing and certification required to navigate the code.
Jump to Energy Conservation Code Hub for; the western slope of Colorado; Aspen, Telluride, Mountain Village, Town of Snowmass Village, Basalt, Carbondale, Pitkin and Eagle County…